鎖定四大應用市場微型化馬達小處見用心
電子產品越來越走向輕薄短小的設計,而微型馬達小而巧的物理特性,正為智慧型手機、無人機、智慧醫療與車用市場,帶來節能、提升效率與強化終端裝置性能的好處,可望促進相關產業發展更為成熟。
台灣馬達產業發展已超過一甲子的歲月,扮演各類型電子電機產業發展的催化劑,不論是大功率輸出的馬達機構或是小功率設計的微型化馬達,皆有相關廠商投入設計,包含台達電、建準、奇鋐、雙鴻、協禧、力致與鴻進科技,都是馬達相關供應鏈的代表廠商。本文將聚焦於微型馬達設計,在終端裝置與電子元件尺寸不斷縮小下,使得微型馬達設計對於尺寸要求更加嚴苛,然而微型馬達尺寸越小則越容易產生增溫,為其研發與突破帶來高度挑戰。舉例來說,智慧手機的影像拍攝應用,在鏡頭的對焦和光學防手震(OIS)部分,就是仰賴微型的音圈馬達(Voice Coil Montor, VCM)予以控制;此外,無人機的雲台散熱控制系統對於微型化馬達尺寸、功耗與製程良率的要求,亦更勝以往。
隨著智慧手機的普及率逐年攀升,現在可說是人手一台智慧手機,其功能不僅用來通話、傳訊息,更重要的是拍出高畫質的照片;為此,手機商也陸續推出雙鏡頭相機鏡頭設計,甚至有些廠商開始朝更多鏡頭的方向邁進。除了透過鏡頭數量的增加,強化智慧手機照相功能外,模組開發商亦採用音圈馬達設計方式,協助自動對焦與光學防手震功能,進而提升智慧手機拍照品質。
事實上,音圈馬達與傳統馬達設計不同,它與結構體(相機模組)整合在一起,因此本身不會迴轉,只能讓鏡頭模組產生偏擺、位移的功能,所以精確來說,又可稱之為微型致動器(Actuator),設計偏向於線圈、磁石和彈片等結構件,主要透過線圈與磁石產生力量,讓鏡頭產生偏擺、水平移動、傾角等,使相機鏡頭即便晃動,亦可修正回來,實現光學防手震功能。
解決磁路干擾 動圈式音圈馬達顯威
工研院機械所控制核心技術組組長彭文陽(圖1)談到,目前主流的相機後置鏡頭大多採用雙鏡頭設計,以單一鏡頭內嵌音圈馬達防手震設計,例如iPhone雙鏡頭設計就是採取這種設計模式。

不過,為什麼有雙鏡頭,但卻只採用單一音圈馬達設計呢?彭文陽分析,音圈馬達可分為兩種設計型式,包含動圈式與動磁式馬達設計。現階段大多相機鏡頭採用動磁式音圈馬達,容易因為手機雙鏡頭間距過近,產生磁路干擾,也基於此,目前大多數的後置雙鏡頭設計僅採用一顆音圈馬達。
為了克服磁路干擾問題,工研院採用全新的磁路架構,設計出一款動圈式音圈馬達,能在後置雙鏡頭內分別加上一顆音圈馬達,此設計能讓雙鏡頭皆具有光學防手震功能,並提升推力比(也就是音圈馬達電能轉換成力量的轉換效率),滿足更加省電的需求。
值得一提的是,雖然動圈式馬達設計能克服磁路干擾問題,但卻也存在著生產良率、尺寸與陀螺儀(Gyro)感測器訊號回傳等挑戰。由於手機鏡頭設計以量產為訴求,若良率不佳則會影響產品性能。再者,音圈馬達的尺寸,也會影響相機模組機構設計,從目前手機後置鏡頭設計來看,鏡頭表面都會有微微突起,原因就是目前的音圈馬達沒有辦法做到很薄,而影響手機外觀。
最後,彭文陽分析,除了磁路干擾外,音圈馬達較少受相關組件干擾,容易產生問題較多在於音圈馬達伺服的動作。由於音圈馬達訊號大多參考內建的陀螺儀感測器,透過陀螺儀感測手機晃動狀態的訊號進行調校。若陀螺儀回傳訊號有較高雜訊,則會影響音圈馬達運作。因此其設計難題,會是在音圈馬達本身的驅動電路設計。
彭文陽談到,工研院全新架構的動圈式音圈馬達,目前良率已達80%左右,門檻主要受限於整體設計的固定方式和黏膠,未來希望能克服挑戰,滿足95~98%的良率水準。此外,該技術現在的外框尺寸可達8×8mm、10×10mm,厚度約3mm,已可讓手機鏡頭表面不再突起。
另一方面,在自拍風潮的興起下,手機前置鏡頭對於光學防手震的需求也逐漸升溫。彭文陽透露,現在已有廠商開始提出規格要求,針對前置鏡頭需要2.6mm以下的尺寸,而該單位延用後置鏡頭的設計模式,已可滿足2.6mm的厚度,未來則是朝向2mm目標邁進。
強化生產良率 微型無刷馬達採半導體製程
架構上,直流微型無刷馬達有好幾個世代,第一個世代的無刷馬達是沒有電刷的直流馬達;第二代則進入到無鐵心時代,內部無矽鋼片設計,因為只要有矽鋼片在其中,則會產生渦流損失困擾,在此時期,皆採用空心線圈,但因空心線圈很難生產,容易墊高生產成本與不良率。為改善此問題,業界馬達廠商開始將微型馬達SMT化,藉以解決渦流損失並改善生產良率。
鴻進科技總經理黃江城(圖2)談到,傳統含有鐵心無刷馬達製作與組裝較為麻煩,通常導磁材料片體需一體沖壓、彎折與捲繞成一具上下極片的圓筒狀,而後需在導磁筒的上下極片間組裝一線圈架,提供線圈繞組,而這樣的機構設計會造成配合轉子運轉不順,並提高微型馬達製造成本;再者,線圈材料的選用也非常重要,目前採用的線圈材質質地非常細,在製造過程中,線與線之間容易打結,造成後續品質控管與良率問題。

基於上述原因,黃江城表示,該公司改良定子結構,提出組件自動化方式,將線圈分組嵌入PCB板上,可多組串接並聯,與半導體零組件同步SMT作業,其良率高達95%。此微型散熱馬達採取的是專利式結構,透過SMT製程技術將馬達核心主件模組化,來改善耗材與製作過程,進而提升精準度與耗能問題,其產品定位為1W以下的區間,目前主要應用於無人機、微投影機和醫療設備等領域,其中無人機應用已與大疆(DJI)合作,用於雲台散熱系統當中,通常一台無人機的雲台散熱系統約採用2~3顆微型馬達。另外,於醫療應用,則是以檢測型醫療器材為主,目前用量正逐年增加。
全球人口步入高齡化社會,照護的需求也愈來愈高,對於相關醫療器材升級的必要性不容或缺,刺激微型馬達在醫療領域的發展,其對於對微型馬達尺寸、效能、低耗電量與精密度的要求更為嚴苛。
客製化馬達設計成主流 醫療照護需求湧現
麥柯昇精密電機(maxon motor)台灣區總經理詹政龍(圖3)談到,微型馬達於醫療應用領域極廣,從達文西機器人、植入式心臟幫浦到外科手工具、義肢及外骨骼等,甚至包括能定時定量為患者注射的胰島素幫浦,都是可布局的領域。對於這些高階醫療應用領域,因為與人體息息相關,無法容許任何的差錯,舉例來說,台灣目前約有200多萬名糖尿病患者,患者自行施打胰島素可能會因劑量不精準、時間不穩定造成諸多問題。因此精密度及可靠度是非常重要,而功耗、尺寸等技術規格的要求仍需視不同應用領域而定。
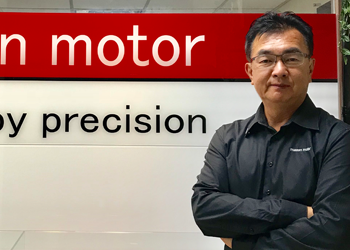
詹政龍分析,針對每種不同應用類型,對於微型馬達的需求也會有所不同,為特定需求找到合適的解決方案,關鍵是提供客製化的產品。該公司有將近80%的產品都是依客戶需求訂製,與客戶合作找出最佳解決方案,這是該公司在微型馬達市場的競爭優勢。
整體而言,微型馬達在醫療應用領域目前應仍處萌芽期,以達文西機器人手術系統來說,1980年即開始研發,2000年於美國上市,至今才普遍應用於全球市場,由此可看出國外醫療應用發展已領先台灣多年。
相較之下,台灣擁有強大的醫療潛力,但受限於廠商投入產品開發的態度仍趨於保守,大多投入國外相似的產品技術,最終將只能以成本為最大考量。若是能應用微型馬達提供的精密度及可靠度,開發更高階及高附加價值的產品,相信微型馬達能在台灣醫療市場更廣泛地被應用。
容易損壞提升汰換率 車用風扇馬達迎商機
除了上述市場之外,安矽思(Ansys)資深應用工程師茆尚勳(圖4)表示,車用市場中,馬達用量最高的地方,可說是安裝於水箱後面的風扇馬達。其因在於,風扇馬達屬於汽車中的碰撞件,容易受到事故碰撞而損壞,不管是前裝或後裝市場,對於風扇馬達的需求極高,因此預計將是車用領域中,馬達最有商機的環節。

不過,茆尚勳也指出,這類型的馬達產量不會是爆發成長,而是透過換機形式的改變,採用控制性、效率更高的電機,取代既有的設計模式,進一步提升需求量。
事實上,早於20年前,車用風扇馬達,採用的是有刷馬達。如今,該設計已從有刷轉變成無刷馬達設計,需要更多定子控制馬達,目前市面高級車種大多採用無刷馬達,預計無刷馬達的引入將成為未來的發展趨勢。
對於車廠而言,在選用無刷馬達設計主要考量分為成本、品質、交期與控制(意指馬達需要與車用系統連結,以有效率執行車用系統發布的指令)等四大要素。茆尚勳分析,無刷馬達有很多材料價格浮動非常大,關鍵原物料包含銅、鐵與磁鐵,如何用最少材料,兼具高效率與微型化設計,將是馬達供應商能否獲利的關鍵所在。舉例來說,銅的價格,每年可能有60~70%左右波動;而磁鐵裡面所選用的稀土元素的萃取,有高環境污染的風險,因此各國也開始管制稀土出產量,間接帶動稀土元素的價格,影響馬達開發商的獲利。
基於此,滿足微型馬達散熱、體積與材料問題,需要有更多實驗與分析工具的導入,以提升產品的差異化,同時解決原物料成本的問題。茆尚勳談到,目前規模比較大的馬達供應商,研發人員相對充足,會有較多的實驗測試馬達樣品,但分析馬達性能,則是馬達設計者較為弱的地方。過去馬達產業來看,大家都可以生產、測試馬達,但如何做出差異化(做得比競爭對手更小),就需要仰賴分析工具。
目前馬達分析可採用電腦輔助工程(CAE)模擬軟體,僅需在電腦上畫出馬達設計圖,並建立材料特性就能預測出物理量,提供算力分析的數據,而Ansys就是提供這類型分析工具的廠商之一。相較於其他競爭對手,Ansys的優勢在於提供一條龍式的分析工具,從最上游的晶片設計到終端裝置,都有相對應軟體測試工具,有效滿足上下游廠商的開發整合工作。
演算法/系統成本/在地服務成關鍵 MCU加速微型馬達發展
恩智浦(NXP)大中華區微控制器與微處理器事業部產品行銷經理李唐山(圖5)表示,對微型馬達而言,工業、汽車與醫療領域是長尾市場,而手機應用市場或許為微型馬達發展的突破點。實際而言,消費電子產品的電機和汽車、醫療應用有很大的差別,手機裡面已經有了用偏心馬達來替代發聲器的設計,無人機裡面使用的是多對極的無感馬達,而汽車中對於馬達和控制器的失效率等有更嚴格的要求。無論如何,即便同樣的應用,不同客戶對MCU的要求,也會有很大差別。

李唐山談到,MCU與馬達的需求一致,都是需要低功耗、小尺寸、高效能和精準度,很多控制裝置或控制面板都要求放在馬達裡面,尺寸要求異常苛刻,對SoC的需求也快速上升。此外,影響微型馬達高效能與精準度的因素,可從三面向來看,首先是MCU提供的演算法優劣;其次為系統成本的優化,比如採用保護更佳的MCU演算法可以支援使用更小容限的MOSFET等;最後是給客戶提供的在地化服務的完善度。當然,製造材料的選擇也會有很大影響,例如如何提高電機的功率密度等,而這就屬於馬達製造商所應面對的課題。
微型馬達在生產製造時,為了解決馬達供應商在生產時個體馬達差異問題,需提高MCU控制器的自我調整性、更好的覆蓋性。為此,李唐山指出,該公司本身具備自己研發的演算法,且提供協力廠商合作的自我調整演算法,在高性價比的Cortex-M4晶片KV系列上,可以快速解決馬達生產製造中的差異問題,簡化客戶在MCU設計上所需時間,而能專注在整體設計上。
馬達作為人工智慧物聯網(AIoT)的執行單元,在很多應用場景都需要作為模組化出現,但是不同應用的技術要求不同,需要更好的普適性,亦為台灣廠商在微型馬達產業的發展機會。